IMA S.p.A.
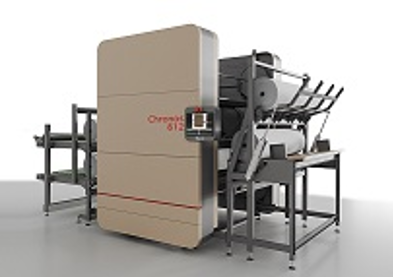
812 AUT. WAREHOUSE 20 ROLLS
Zum Produkt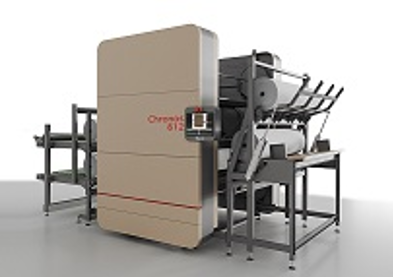
812 AUT. WAREHOUSE 20 ROLLS
Zum Produkt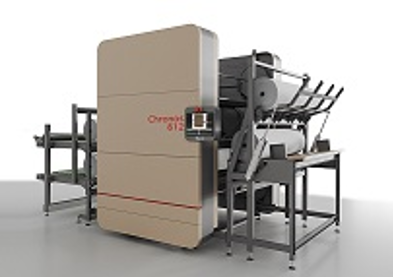
812 AUT. WAREHOUSE 20 ROLLS
Zum ProduktAdresse
IMA S.p.A.
Via Piantada 9/A
25036 Palazzolo Sull'Oglio Brescia
Italy
Telefon+39 030 648 5011
Fax+39 030 648 5099
Entdecken Sie mehr von uns
Über uns
INNOVATIVE INTEGRATED SYSTEMS FOR
COMPLETE MANAGEMENT IN CUTTING ROOM
Since 1977 the name IMA has been synonimous with quality and technological innovation.
For 45 years our company has dedicated itself to the production of automated machinery and equipment (specialized in handling and management systems of cloth rolls, spreading solutions, labelling and automatic cutting machines and software programs for the complete organization of the cutting room) for the garment industry and not only.
Thanks to the dedication of our personnel we’ve been growing each year and nowadays we stand as world leader in the cutting room equipment industry. Our decades-long experience, mixed with the energy and the talent of a young and driven team, is what allows us to steadily keep walking on the road of innovation.
After being pioneers of digital technology with the creation of the first full-digital spreading machine we are now pioneers of Industry 4.0 with our latest creation: “Syncro Cutting Room”.
Specialized in handling and management systems of cloth rolls, spreading solutions, automatic cutting machines and software programs for the complete organization of the cutting room.
Unsere Produktgruppen
- CMT (Cutting, Making, Trimming)
Downloads
Dokumente
Keywords
- AUTOMATIC CUTTING MACHINES
- INTEGRATED SYSTEMS FOR CUTTING ROOM
- SPREADING AND UNROLLING MACHINES
- SYNCRO CUTTING ROOM
- LABELLING MACHINES
Unsere Produkte

Tempest Plus 921.30 - High precision for small series productions
Tempest Plus 30 - Automatic cutting machine for lays up to 30 mm compressed according to the type of fabric to cut. Structurally designed to achieve the highest level of performance and to reduce downtime during processing with high dynamic performances. The software of the machine is installed on a PC on board, increasing its efficiency and productivity, thanks to intuitive and flexible applications. Available as standard the possibility of storing an unlimited number of cutting profiles to be load if necessary. ntegrable for Industry 4.0 and IMA Syncro Cutting Room System. The innovative management of the vacuum system guarantees a reduction in consumption with the same performance. The digital technology totally based on the ETHERCAT communication protocol allows to check the status of the machinery in real time, with self-diagnosis functions and automatic options for adjusting the performance based on the type of work in progress.
Among the most important innovations we find gantry management of the bridge movement, management of differentiated pressure of the utilities most involved in the cutting process, touch screen placed on the bridge to allow the operator greater ease of intervention, Equipped with an inverter on all the utilities, an eco-friendly management of each motorization is ensured.
TECHNICAL FEATURES:
- Cutting window length: 175 cm.
- Cutting height: from single lay up to 30 mm of compressed fabric
- Installed power: 22 kw
- Power consumption: 6 kw
- Temperature from 10 ° to 60 °.
- Umidity from 30% to 80% without condensation.
- Voltage 400 V 3 PH 50/60 Hz.
- Weight: ~ 2500 /2700 kg
SOFTWARE SPECIFICATIONS
The software has been re-adapted in its layout and in supporting the
new mechanical features introduced.
- HMI (Human Machine Interface) sistem, designed by IMA. Very easy
and intuitive build on a color touch screen.
- Possibility to transform the polygonal system to the cartesian
geometry system, for better movements thanks to the optimization of
ISO cutting file.
- Adaptive movements functions of the machine while performing
curves or critical angles, then use zero buffer on marker..
- Possibility to manage symmetries of all patterns.
- Possibility to recognize and manage common lines.
- Automatic research of the starting point of the pattern.
- Possibility to change the cutting direction of the pattern.
- Different strategy of cutting for windows management, adjustable
according to every kind of fabric and marker, with cutting path optimization.
- Possibility to manage, convert and transform all kind of notches
(normal, V notch and fly notch).
- Possibility of merging different markers, to delete a single pattern
inside the marker and to manually move the pieces with a collision
control to optimize the workflow.
- Possibility of markers elaboration with graphic and statistic reports.
- Possibility to create and print a HPGL file for plotters from ISO file.
HARDWARE SPECIFICATIONS
- HMI software for machine management and CAM for cutting file
processing are pre-installed on the PC supplied as standard.
Windows 10 as operating system.
- Controlled vacuum by means of PID and double inverter
simultane-ously controlled, optimizing the power consumption.
- Mitsubishi command technology of engines of the latest
generation.
- Conveyor belt of loading and unloading perfectly synchronized
with the automatic cutting machine.
- Blade strainers, to increase the cutting quality.
- Blade speed up to 4000 rpm.
- Gantry ax for the movement of the bridge, increasing its ability of
control and precision as well as perfor-mance.
- Touch screen on the side of the bridge to easily manage the
machine even away from the PC.
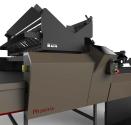
890 Spreading and Unrolling machine
IMA 890 - Automatic spreading and unrolling machine IMA “Phoenix” series.
Fabric Feeding, Tension Free and Automatic Braking systems digitally controlled.
Equipped with onboard touch-screen to control spreading operations.
Auto-diagnosis function. Lowered cradle to facilitate fabric roll change.
Programmable bi- directional cutting device. Automatic edge alignment and automatic stop for roll change.
Fully automatic spreader adapted to be interfaced with planning offices and CAD systems. Possibility to program on the touchscreen spreading speed and acceleration. Automatic knife box lift.
Standard spreading is face up and zig-zag without end cuts and without clamps. Face to face spreading is available as optional. Suitable for even/random step spreading.
POSSIBILITY TO STOP THE SPREADER AND SPREADING AS UNROLLING MACHINE (SINGLE PLY)
TECHNICAL SPECIFICATIONS
- Spreading speed: up to 100 m/min
- Lay Thickness: 20 cm
- Voltage: 400V / 3 / 50 Hz
- Capacity: 150Kg
- Roll Diameter: 50cm
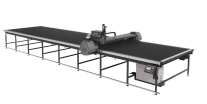
908 – POLARIS The newest digital labelling system
908 POLARIS is IMA labelling system for recognizing cut-out fabric bundles which avoids markers printing, allowing drastic cut of paper, ink costs and also high abatement of environmental impact.
The system automatically applies adhesive labels to the top of the lay, giving the necessary information in order to recognize the parts of the model and of the bundle.
It is equipped with a thermal printer and can use adhesive labels of various sizes, depending on the quantity of information to be printed and the size / type of font or barcode you choose.
An optional software can automatically correct the position of the labels, placing them exactly at the center of the patterns or allowing the operator to move them at his own discretion. It is possible to add, remove, duplicate and modify each label.
The system is integrated into any spreading line and runs independently and at the same time of other machines, optimizing the dead times. It’ s compatible with any CAD system because it uses HPGL / HPGL2 file format used for plotter printing.
Technical features:
– Possibility to view the status of functioning of labelling machine
– Separate management of users and groups; authentication by user name and pass-word. Possibility of customization of graphic interface according to the requirements of the various groups
– Production data feed-back
– Detailed view of all data related to the works performed (file name, length, height, number of labels, total time, etc.)
– Data selection according to one or more filters arbitrarily applied
– Data printing and exporting in Microsoft Excel and text formats
– Composition of pie charts for data comparison
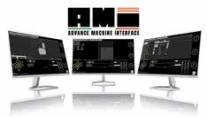
AMI - Advanced Machine Interface
AMI is the name of the new software program HMI which manage IMA automatic cutting machines of new generation.
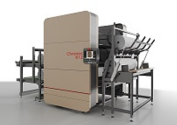
812 AUT. WAREHOUSE 20 ROLLS
The automatic warehouse Chronos 812 has been designed for handling any kind of fabric rolls. The maximum dimensions of the fabric rolls are:
- Diameter = 400mm
- Fabric height 1600mm
- Roll weight 35 kg
The machine is made by three stations:
- Preloading / unloading station: it takes care of managing the rolls entering the warehouse (positioned on the lower belt) through a FIFO type queue, up to a maximum of 9 pieces, which will be stored inside the warehouse itself; it also guarantees the unloading of the pieces leaving the warehouse. Both stations are made with PVC belts, directly controlled by the warehouse software.
- Management warehouse: it is the actual warehouse, where fabric rolls are allocated in cradles, handled using a chain guided revolver system. The handling phase both in and out of this station is managed by the warehouse software.
- Interfacing station with spreader / unroller: this station automatically picks up the pieces returned by the spreading (with a special roll rewinding cycle) and gives the next one to the spreading to continue the process.
The warehouse structure can be customized, according to the number of rolls to manage, both in height and in length. The modularity of the machine also allows to manage rolls of different diameters. The strength of the 812 Chronos machine consists in making the next roll immediately available before the unloading operation of the previous one is completed. In this way, the dead times of processing are reduced, increasing the productivity of the spreading line and the related cutting connected to it. Chronos can manually manage the work queue (taking charge of a sequence of fabric rolls to be processed) or it can acquire the work queue to be created using the planning & management software. Included within IMA lines, the 812 Chronos warehouse meets the requirements of industry 4.0. It is also interfaceable with other external systems (to be estimated case by case).