Sip-Italy S.r.l. Società Benefit
Address
Sip-Italy S.r.l. Società Benefit
Via Maestri Del Lavoro 12
37059 Zevio Verona
Italien
Telephone+39 045 1117 0246
Fax+39 045 605 1645
Discover more from us
Follow us on
About us
SIP-ITALY is specialized in the development and production of automatic units for Jeans & Trousers.
Our passionate team has more than 30 years working experience in this field. Our plant is located in Verona, north of Italy.
We focus on “A top class” apparel industries, interested in the best product of engineering, quality and daily productivity output.
We achieve the goal to manufacture friendly use automatic work-stations, with best ratio in terms of productivity and versatility at the lowest running cost.
Most of our automatic workstations are equipped with common electronic hardware and standard sewing heads.
It is the best technical solution, giving incredible benefits to our users.
Best products made with best supply chain! This is one strenght of our business strategy.
Thanks to management credibility and reputation, we are proud to have a successful technical cooperation with the major Japanese sewing machine manufacturing companies of this field.
The majority of our products will be linked with network connectivity soon, a new era of industrial sewing machines.
In this way for example, the customer can download productivity data to set a maintenance programme, to get error message or downtime alarm signal, to transfer software or sewing pattern. This is the Factory 4.0, actual benchmark for all Industries.
We are the game changer of Jeans Supply chain, FACTOR-HIT by SIP-ITALY is actually the best proposal for complete turnkey solution for new reshoring jeans factory in Europe and USA
We count several history cases in Europe and USA
FACTOR-HIT is a turnkey solution where we bring all our experience and know - how in jeans apparel production process together with best advanced technology.
We like to merge our know-how with the customer production management. Our turn key project brings the level of cooperation between us and the customer on different scenarios. In this way, we get involved in different phases of new factory set up or upgrade of existing ones.
- Complete support in the evaluation of factory site;
- Layout of cutting and stitching floor;
- Production flow chart study;
- Time and method efficiency analysis with efficiency goals;
- Machinery set up, training for sewing machine operator;
- Implementation and start of the garment production;
- Follow up of the production.
AFTER-SALES SERVICE
We have a dependable support system close to our customers to assure satisfactory operation of the units.
The confidence in the back-up service depends on the engineering of the units.
- Common electronic hardware and software for standard and automatic sewing machines;
- Standard sewing head;
- Standard consumable parts;
- Standard pneumatic components available in all markets;
- Certificate manufacture process for mechanical parts attachment;
- Our units can be controlled in remote for diagnostic check and software updates;
- Sewing pattern for major units can be generated by Brother Software on PC;
- Freedom to outsource at the cheapest price, just on time, not depending on us;
SIP - ITALY units are 4.0 workstation , customer can trace in remote all live productivity data, all error data messages, production data, running time and downtime.
Our units are not sophisticated exhibition products. Automatic work stations must be simple, easy to use by no-skilled operators and the adjustments are made by technical maintenance staff. Our engineering team is the same who regularly visits the customers. R&D and people in the field are the same team.
Reliable quality
In accordance with the ISO 9001 quality management system and under our strict control, we provide top-quality industrial sewing machines in the industry.
Sewing machines with less noise
Taking particular care of vibration, noise quality, and quietness in the machine operation, we produce a comfortable working environment for all operators.
Energy efficient sewing machines
We offer our sewing machines with low power consumption and running cost, employing compact motors developed in-house to best fit the machine heads.
More about us
Special Interests
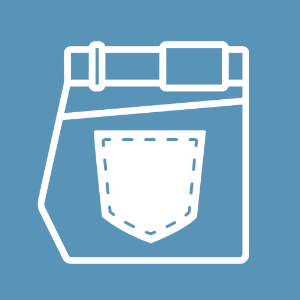
Keywords
- automation
- sewing
- reshoring
- fashion
- denim
Our Products
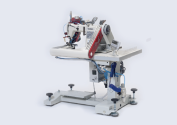
9280SPV
FEED OF THE ARM UNIT
Feed of the arm unit, 3 needle, chain stitch, special design for lap felling and/or double-lap seaming like yoke sewing, back seat, in-seam and side-seam operations for jeans, casual trousers in general, working clothes, denim jackets, etc.
HIGHLIGTHS
- Direct Drive Electronic Puller, transmission by Step Motor, ensures a perfect synchronization with the sewing head;
- Perfect timing means no waves in the seam, no puckering, perfect stitch quality!;
- Sensor detecting the thickness: the work-station automatically adjusts the pressure on the presser foot bar along the seam in order to avoid to skip stitch or un-constant stitch length;
- Automatic dynamic speed control on thick area;
- Automatic dynamic presser foot edge device controlled by thickness sensor for constant seam margin on crotch – back rise area;
- Automatic pneumatic chain cutter controlled by photocell;
- Common electronic servomotor as other units of Sip-Italy range;
- Sewing head made by Brother Japan;
- Dynamic take up lever for attractive balloon stitches even with thick sewing threads;
- Full pushbutton operation. The stitch length can be changed simply by pressing a button and changing the parameter on the console. Very easy setting!;
- Reverse lap folder made in Italy;
- Standard consumable parts, available in all markets with lowest running cost.
PRODUCTIVITY
Yoke seam:
from 200 to 300 pairs of jeans / 1 hour
Back rise:
from 250 to 350 pairs of jeans / 1 hour
Inseam sewing:
from 130 to 180 pairs of jeans / 1 hour
Side seam sewing:
from 100 to 130 pairs of jeans / 1 hour
TECHNICAL DATA
Sewing head utilized:
three needle chain stitch unit, heavy duty, manufacture by Brother, model 9280, sub class 5 or 7, Made in Japan
Max sewing speed with all thickness of fabric: 4.500 rpm
Stitch length: from 1 to 5 mm
Standard needle gauge: 6.4 mm = 1/4”
Presser foot lifter: pneumatic
Motor: standard servo motor EFKA, made in Germany
Power supply and air consumption:
0.6 Kw - 220 Volt, mono-phase 50/60 Hz
0.3 liter/cycle at a pressure of 5.5 bar
Size and weight of the workstation:
96 x 73 x 140 cm – 140 Kg
OPTIONS
- Option needle gauge: 4.8 - 5.6 - 7.2 - 8.0 - 9.6 mm;
- Automatic dynamic presser foot edge device controlled by thickness sensor Item Code SIP.A.000328;
- Mechatronic device for super stretch fabric Item Code: SIP.A.000856;
- Folder for super stretch made in Italy Item code GO 180SPE;
- Extended plate for reverse yoke
- Item Code SIP.A.000440.
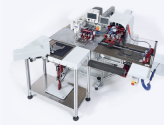
CP341-FG-SIP
FULLY AUTOMATIC PROGRAMMABLE UNIT FOR COIN POCKET AND FACING ATTACHING OPERATION - EQUIPPED WITH COLD FOLDING GROUP
Automatic workstation for coin pocket and clean lock stitch facing attaching operation.
The same unit can be utilized as standard back pocket attaching operation for kids wear garment.
HIGHLIGTHS
- Clean lock stitch of the facing: new “must” for premium brand, value added style product at lower production cost!
- Fashion watch-coin sewing programme;
- Folding and attaching on the same workstation;
- Cold folding device is the unique solution for stretch denim fabric;
- Original Brother sewing head, standard X-Y technology, hardware & software by Brother Japan, same as other Brother units;
- No extra workers and helpers to manage the Coin pocket and facing operations: instead of marking, folding and different sewing stations, everything is made in one workstation;
- Digital sewing thread tension;
- Presser foot height controlled by step motor, editing sewing programme;
- Local pocket jig production by user in all countries of the world;
- Automatic device for quick pocket jig change;
- Friendly use, no skill operator and helpers required;
- LED lights for panel positioning;
- Multicolor touch screen 5.6” programmed for multi languages;
- All standard pneumatic valves and cylinders by SMC;
- Lowest running cost. Freedom to outsource the standard consumable spare part in all market locally at the best price and delivery.
PRODUCTIVITY
Coin pocket operation with 80% efficiency:
360 pcs / 1 working hour
8 seconds / cycle
Left and right facing operations
with 80% efficiency:
265 pairs / 1 working hour
6 seconds / cycle
Coin pocket, left and right facing operations:
120 pairs / 1 working hour
1.000 pairs / 8 working hours
TECHNICAL DATA
Min and Max coin pocket finished size:
from 60 x 60 mm to 120 x 120 mm
Min and Max facing finished size:
from 60 x 60 mm to 195 x 160 mm
Sewing head utilized:
Brother model BAS-341 H serie,
NEXIO Technology, single needle lock stitch, direct drive, eco energy product
Max sewing speed:
2.800 rpm
up to the stitch length of 3.5 mm
Power supply and air consumption:
220 Volt, mono-phase 50/60 Hz
1.0 Kw
30 liters/cycle at a pressure of 5.5 bar
Size and weight of the workstation:
145 x 191 x 203 cm – 400 Kg
OPTIONS
- PS-300B Sewing data programming software by Brother for creating, editing, setting and converting of sewing data;
- IoT Software for FACTORY 4.0 network connectivity by Brother.
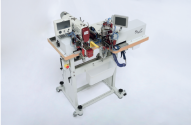
LS915H-SIP
AUTOMATIC PROGRAMMABLE BELT LOOP SETTER UNIT
Automatic programmable belt loop setter unit for cutting, folding and attaching of the patch loop in one operation. User is able to make on board all kind of bar-tack sewing designs by consolle or by pc.
HIGHLIGTHS
- Smallest sewing head arm in the market suitable for only 12 cm diameter waist length;
- Wider space between sewing head and loader for better handling and garment rotation;
- Unique two needle loop setter unit equipped with double needle bars: more sewing strength ! more versatility!;
- Smart loop joint detector device with shortest wasted fabric lenght;
- Friendly use, no skill operator and helpers required;
- Original standard X-Y technology, hardware & software by Brother Japan, same as other Brother NEXIO Technology units;
- Large-capacity memory capable of storing bulky data, up to 512 programs, 500,000 stitches;
- Compensatory presser feet with double pressure logic function;
- Multicolor touch screen 5.6” programmed for multi languages;
- IoT Software for FACTORY 4.0 for cloud connectivity of production data, error message, software update, remote control and more;
- Height of the stand adjustable by operator;
- Cross and straight loop cutting device without optional parts up to 30 mm;
- All standard pneumatic valves and cylinders by SMC;
- Lowest running cost. Freedom to outsource the standard consumable spare part in all market locally at the best price and delivery.
PRODUCTIVITY
Complete cycle time:
11 seconds – 5 loops
Average production with 5 loops:
200 pairs / 1 working hour
1.500-1.700 pairs / 8 working hours
TECHNICAL DATA
Sewing head utilized:
Direct drive Brother model T-8720, double needle lock stitch, large rotary hook size
Max sewing speed:
2.800 rpm
Power supply and air consumption:
220 Volt, mono-phase 50/60
1.0 Kw
1.5 liter/cycle at a pressure of 5.5 bar
Size and weight of the workstation:
125 x 95 x 140 cm – 245 Kg
OPTIONS
- Extended presser feet for 30 mm loop width – item code SIP.A.000739
- PS-300B Sewing data programming software by Brother for creating, editing, setting and converting of sewing data;
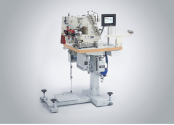
6044-SPVCH
AUTOMATIC WAISTBAND UNIT
Automatic waistband unit, all chain-stitch, equipped with triple electronic puller devices, two on top side and one on bottom side. The unit attaches a waistband in automatic way, with cutting at the beginning and at the end leaving the waistband edges open. All parameters can easily be set by touch screen. Our unit sews a pre-formed continuous waistband by specify folder for all kind of trousers, fashion or basic jeans and jacket.
HIGHLIGTHS
Electronic puller controls by independent step motor, for the best anatomic “banana” shape even with straight cut;
Top sewing quality specially for double curved waistband;
Super Flexible Patented multi needle gauge with the freedom to select needle gap 1/8" or 1/4" for different measures;
All functions programmable by touch screen;
Automatic cutting at the beginning and the end of the trouser;
No helpers and skill workers required;
Device to release the loopers for thread in operation;
Common control box as other Sip-Italy units;
Common spare part available in the local market;
Kansai sewing head, cylinder arm, made in Japan, full oil lubrificated.
PRODUCTIVITY
Complete cycle time:
10 seconds
Average production:
225 pairs / 1 working hour
1.800 pairs / 8 working hours
TECHNICAL DATA
Two options for Standard needle gauges available with the units:
a. 1/4”-1”-1/4” ; four needle; ext. needle 1”1/2 ; needle to needle 1/4”
b. 1/4-7/8”-1/4”; four needle; ext. needle 1”3/8; needle to needle 1/4”
Please specify with customer PO
Sewing head:
model FBX-1104
made by Kansai Industries Ltd Japan
Max sewing speed:
4.000 rpm
Power supply and air consumption:
220 Volt, mono-phase 50/60 Hz
0.5 Kw
0.3 liter/cycle at a pressure of 5.5 bar
Size and weight of the workstation:
105 x 75 x 140 cm – 150 Kg
OPTIONS
Option multi-needle gauge, 1/4" gap:
3/4” – 1”– 1”1/4 – 1”1/2 – 1”3/4 – 2” – 2”1/4
item code SIP.A.000245;
7/8” – 1”1/8 – 1”3/8 – 1”5/8 – 1”7/8 – 2”1/8
item code SIP.A.000246;
Patented multi-needle gauge system.
Same gauge can work for 1/8” or 1/4”
gap with different following measures:
3/4” – 1”– 1”1/4 – 1”1/2 – 1”3/4 – 2” – 2”1/4
item code SIP.A.000772.
Special folders, single or double, straight or curved bands made in Italy;
Quick change folder device item code SIP.A.000282;
Pneumatic single needle skip
stitch seam device item code SIP.A.000805;
Supplementary extra waistband rail item code SIP.A.000146;
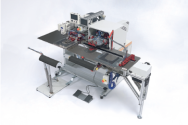
PS342-FG1SIP.V2
FULLY AUTOMATIC PROGRAMMABLE POCKET SETTER UNIT FOR JEANS & PANTS
UPGRADE WITH COLD PLASTIC FOLDING GROUP
Automatic workstation for pocket folding and attaching in one operation. User doesn’t need to utilize any pocket creaser unit. The unit can be upgraded into two sewing head configuration.
HIGHLIGTHS
- Folding and attaching on the same workstation;
- Cold folding device is the unique solution for stretch denim fabric;
- No extra workers and helpers to manage the pocket pressing unit, with saving of area,energy and generally reduction of the running cost;
- Original Brother sewing head, standard X-Y technology, hardware & software by Brother Japan, same as other Brother units;
- Local pocket jig production by user in all countries of the world;
- Automatic device for quick pocket jig change;
- Friendly use, no skill operator and helpers required;
- Digital sewing thread tension;
- Presser foot height controlled by step motor, editing sewing programme;
- Large-capacity memory capable of storing bulky data, up to 512 programs, 500,000 stitches;
- Multicolor touch screen 5.6” programmed for multi languages;
- All standard pneumatic valves and cylinders by SMC;
- Lowest running cost. Freedom to outsource the standard consumable spare part in all market locally at the best price and delivery.
PRODUCTIVITY
Complete cycle time:
10 seconds – regular pocket size
Average production:
120 pairs / 1 working hour
960 pairs / 8 working hours
OPTIONS
Retractable inner clamp for different small size:
- from 90 x 90 mm item code SIP.A.000781;
- from 70 x 70 mm item code SIP.A.000746;
Folding group for different pocket size:
- Small pocket size folding group for pocket size below 128 x 149 mm item code SIP.A.000492;
- Large pocket size folding group for pocket size larger than 215 x 220 mm item code SIP.A.000487;
LED lights for back panel positioning item code SIP.A.000642;
Quick change for folding group jig item code SIP.A.000718;
PS-300B Sewing data programming software by Brother for creating, editing, setting and converting of sewing data;
IoT Software for FACTORY 4.0 network connectivity by Brother.
TECHNICAL DATA
Standard setting
Min and Max pocket finished size:
from 128 x 149 mm to 215 x 220 mm
optional retractable inner clamp and folding group devices for smaller and wider pocket size up to 250 x 244 mm.
Sewing head utilized:
Brother model BAS-342 H serie, NEXIO Technology, single needle
lock stitch, direct drive, eco energy product
Max sewing speed:
3.000 rpm
up to the stitch length of 3.5 mm
Power supply and air consumption:
220 Volt, mono-phase 50/60 Hz
1.0 Kw
30 liters/cycle at a pressure of 5.5 bar
Size and weight of the workstation:
205 x 165 x 140 cm – 450 Kg